“Key technological breakthrough” in recyclable wind turbine blades.
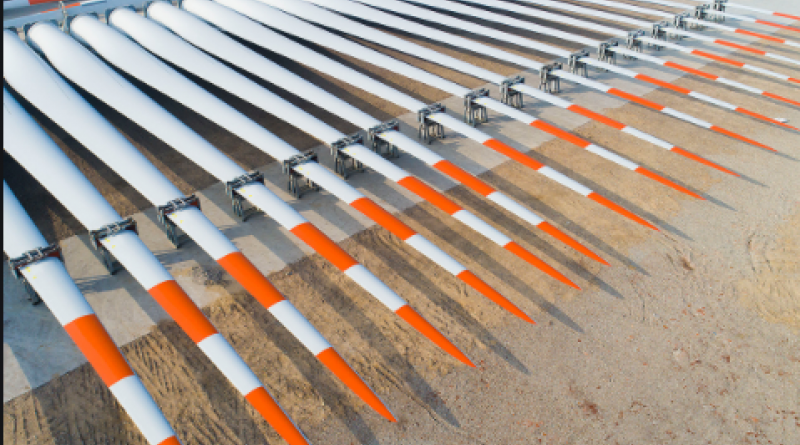
One of the world’s largest wind turbine manufacturers said yesterday it has made a “key technological breakthrough” that would allow it to stop sending old turbine blades to landfills — an issue cited by experts as a growing concern for the industry.
Vestas Wind Systems A/S, ranked last year as the biggest global producer of turbines by the Global Wind Energy Council, has previously said it wants to produce “zero-waste” turbines by 2040, meaning all components would be recycled or reused once a turbine is decommissioned.
The biggest technical hurdle to that goal is figuring out what to do with the blades, which are usually made with nonrecyclable materials. It’s also a challenge for policymakers and wind companies beyond just Vestas: The mammoth blades can stress landfills for space, and in 2030, about four times as much wind power will be needed globally as in 2020, according to an International Energy Agency analysis published today.
Now, Vestas says it has the technology to make its blades recyclable. It works by disassembling two common materials — a kind of resin known as epoxy and fibers made of glass or carbon — effectively returning both to their “virgin,” pre-fusion state and allowing them to be incorporated into other products, according to the company and its research partners.
Within three years, the company is aiming to commercialize it, with the help of a newly launched partnership, known as the Circular Economy for Thermosets Epoxy Composites (CETEC), that includes two Danish universities and an investment fund.
19 May 2021
IEEFA