Are vertical-axis wind turbines really the future.
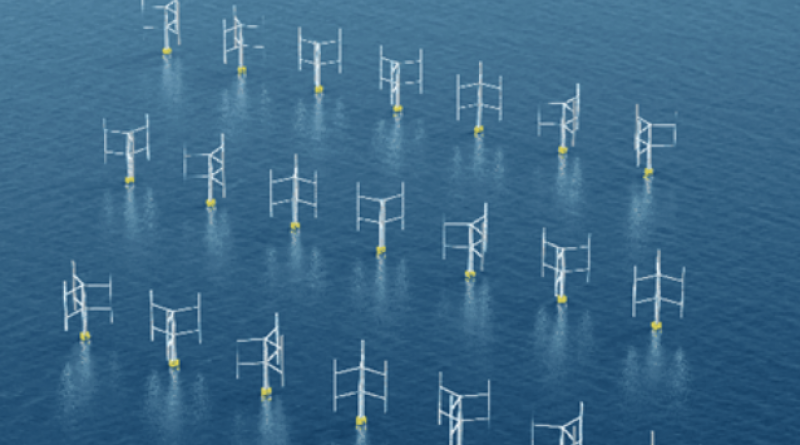
New research suggests VAWTs could surpass current ofshore giants. Eize de Vries talks to an aerodynamics expert who disagrees.
Recently published research by Oxford Brookes University suggests that H-shape Darrieus vertical-axis turbines (VAWTs) installed a certain way could outperform “traditional propeller-type” wind turbines or HAWTs in wind farms.
When set closely interspaced in pairs, VAWTs increase each other’s performance by up to 15%, the UKbased institute said in its press release, triggering much media attention. Business publication Forbes wrote in May: “A recent discovery by engineers of Oxford Brookes University’s School of Engineering, Computing, and Mathematics could change the design of ofshore wind farms forever.”
But how realistic are predictions gained from two-dimensional modelling of theoretical VAWTs with 20- metre rotors compared with current “traditional” ofshore giants? And who will develop and build them?
Computer simulation
The study, “Numerical modelling and optimisation of vertical-axis wind-turbine pairs: A scale-up approach” was originally published in Elsevier’s Renewable Energy journal in March. It is reported to be the first to comprehensively analyse many aspects of wind-turbine performance, with regards to array angle, direction of rotation, turbine spacing and number of rotors.
The university’s research team, led by Iakovos Tzanakis, a professor in technology, design and environment, used extensive computer simulation for the in-depth study “This study evidences that the future of wind farms should be vertical,” Tzanakis said. “Vertical-axis wind farm turbines can be designed to be much closer together, increasing their efciency and ultimately lowering the prices of electricity. In the long run, VAWTs can help accelerate the green transition of our energy systems, so that more clean and sustainable energy comes from renewable sources.”
The researchers argue that VAWT’s in wind-farm array do not sufer from HAWT-related turbulent wake issues created by the first row, which decrease the output of the rows of turbines behind by up to 40%. Using vertical- rather than horizontal-axis machines would not only eliminate this problem, they suggest, but the VAWTs would actually enhance each other’s performance.
Two similar-size rotors were used for the research, with the second rotor placed the length of three rotor diameters downstream. The maximum increase in power output — compared with two units each operating in isolation — was achieved with the second rotor placed at a 60-degree array angle (ß) to the prevailing wind direction.
Another variable the team introduced was letting the two rotors either co-rotate in the same direction or counter-rotate, whereby the counter-rotating pair performed better only at smaller array-angles of around -30 to +30 degrees. Minimum power output is logically achieved when the wind blows directly over the two rotors positioned in line relative to the prevailing wind direction (0 degrees).
Finally, a two-dimensional space was an integral part of the computational fluid dynamics (CFD) modelling properties.
Performance augmentation
Lead author Joachim Toftegaard Hansen explained why the team chose an H-type Darrieus rotor shape with a 20-metre rotor diameter for the analysis: “Other studies have verified similar performance augmentations for other Reynolds numbers [to predict flow patterns] too. This is something we are possibly interested in investigating in our future studies, analysing the efects of turbine size.”
A key question is whether such envisaged VAWT-based ofshore wind farms could indeed propel them at par with the latest HAWT-technology — which is now at the 11-15MW scale and has 30 years of cumulative marine experience under its belt.
Aerodynamics expert Jens Nørkær Sørensen is a professor in the wind-energy department at the Technical University of Denmark (DTU) who worked with VAWTs in the past. He questions the scientific design basis of the Oxford Brookes research efort, the design set-up and the outcomes on which the conclusions are based.
“My objections concentrate on three main points. The first is about the use of a two-dimensional shape for the CFD flow model. Wind flow in a wind-farm array should, in my view, always be studied from a three-dimensional perspective because the mixing of fresh high-energy wind from the upper, outer layers with ‘depleted-energy’ wind flow inside the wind-farm boundaries is of key importance to continuously regenerate energy for generation in downstream turbine rows.”
This essential mixing of wind flow inside wind farms with HAWTs takes place automatically, because the spinning blades “sweep” fresh air from upper wind layers into the array during each individual rotor revolution. Tip heights of the latest and largest ofshore turbines now reach up to 250 metres, and will soon hit 300 metres and more. At these altitudes wind speeds and thus energy in the wind are high.
No wind mixing
In contrast, with VAWTs the rotor rotating-axis is vertical, so the rotor thus always spins in the same plane, Sørensen explains. As a result, there is no mixing of fresh and already “depleted-energy” wind flow, and this “used” air remains inside the wind-farm array, with a substantial negative impact on potential power production in all further rows downstream.
His second criticism is linked to the research set-up involving only two rotors. These are, according to the report, “positioned in a rotating region within a larger rectangular domain with stationary walls top and bottom, a velocity inlet and a zero-gauge pressure outlet.” This selected set-up with two turbines, plus the flow boundary conditions is depicted in the chart below from the report.
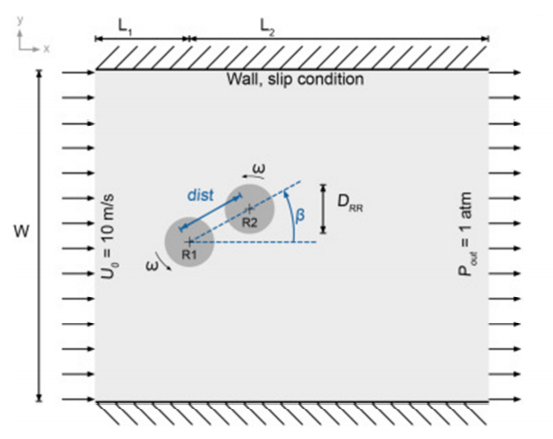
This overall research concept contains several other fundamental design flaws, Sørensen believes.
“My third point is that it ignores real-life conditions inside a wind farm, whereby such ideal uniform wind flow conditions with unilateral wind direction do not exist. An inter-related research-design error is that it does not consider the complex, continuously varying wind-flow interaction efects with other turbine rows downstream,” he says.
“Taking all these flaws and errors into account, the claimed benefit of up to 15% power augmentation for closely interspaced VAWTs in wind-farm arrays looks highly unlikely,” Sørensen says.
“Finally, HAWTs can be located much closer to each other in wind farms because of their superior aerodynamic efciency, therefore they ofer a significantly higher yield per area (see Vertical- versus horizontal-axis turbines). Producing electricity at the lowest lifecycle-based LCoE remains key”, he concludes.
Huge instant leap
The pathway to commercialisation of VAWT technology up to state-of-the-art HAWT levels was not covered in the study but will be far from easy with many hurdles (see and uncertainties.
Two (UK) companies, Vertax Wind and Wind Power’s Aerogenerator X (below), introduced ofshorededicated 10MW VAWT-concepts in 2009-2010, but neither reached the prototype stage. Both designs come with very high specific power ratings: 649W/m2 for the Vertax 10MW design (140-metre rotor diameter and 110-metre blade length), and roughly 1,050W/m2 for the Aerogenerator X
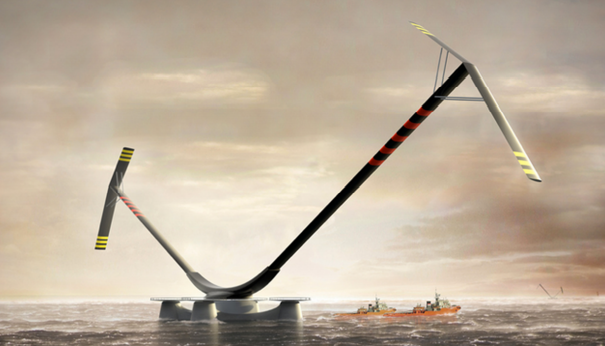
In comparison, the HAWT-type Siemens Gamesa SG 11-200 DD comes in at 350W/m2, with the SG 222 DD (in 14MW mode) at 362W/m2.
To develop vertical-axis turbines into full-scale competitive commercial concepts matching the latest and largest 12-15MW HAWT flagship category, technology companies are basically starting with a track record gained largely with kilowatt-class turbines and generally only limited onshore experiences.
Such comprehensive product development processes will require a huge instant wind technology scaling leap and a massive industrialisation efort. It also requires large, strong parties with long-term commitment and deep pockets to take it to completion and then fast-track it to commercial ramp-up, leading to bankability and beyond.
Vertical- versus horizontal-axis turbines
A major benefit of vertical-axis wind turbines (VAWTs) compared with their (upwind) horizontal counterparts (HAWTs) is that they can draw wind from all directions while not needing a yaw system.
A main disadvantage compared with modern, large-scale HAWTs is much lower aerodynamic efciency. The Oxford Brookes University report states a maximum pressure coefcient (Cp) in the 35-40% range, compared with nearly 50% for HAWT, both for turbines operating in isolation. Vertax (pictured below) states a Cp of 38-39% design objective.
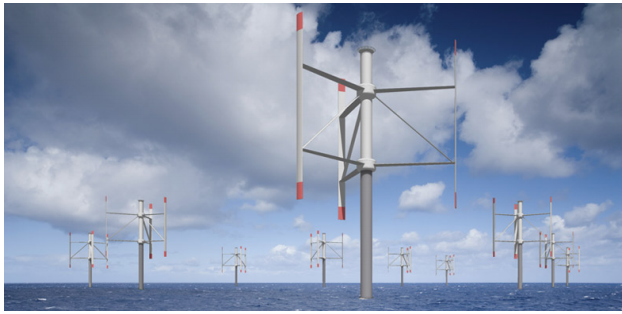
A major consequence is that the specific power of VAWTs must be substantially lower to achieve similar energy production to compensate for their reduced aerodynamic efciency. This means there is an inherent need to fit a bigger rotor per megawatt within the same wind classes they are designed for and the required annual full load hours.
Some VAWT designs lack self-starting capability as well, requiring an external power source (with associated energy loss) during each starting-up action, either a dual-mode generator-motor electric machine or two separate devices.
Historic non-self-starting small-scale VAWT rotors were sometimes fitted with a small Savonius dragtype rotor inside, but this would always be at the expense of total system aerodynamic efciency.
Another VAWT-challenge is power output control:
-For stall-type variable-speed designs with a fixed blade angle, an output control option is rotorspeed control whereby a dual-mode generator-motor maximises and retains the rated output level. The main disadvantage — and safety concern in some experts’ views — is the lack of an aerodynamic braking system found in modern pitch-controlled HAWTs (three independent fail-safe aerodynamic brakes). An interlinked challenge is that continuous switching of the load direction during turbine operation in the rated power range could accelerate materials fatigue and trigger premature failures.
-With pitchable blades as an alternative solution, each blade is attached to support arms and bearings so that it can rotate. This requires at least one or more bearing supports and pitch systems for long blades, adding complexity, Capex and, likely Opex as well, compared with HAWTs. This is because the bearings and pitch systems are located in difcult-to-access exposed locations. They could be distanced around 110 metres from the rotor centre for a fictive 11MW H-type Darrieus turbine with a 220-metre diameter, 175-metre long blades and a 286W/m2 power rating.
-A third challenge is that the full VAWT-rotor plane always directly faces the wind and stopping plus locking the rotor during high-wind conditions would require a large and costly braking system. Past eforts to build H-type Darrieus turbines with reefable or foldable rotors proved either too expensive or were unsuccessful for other reasons, such as fast wear in the pivot points due to, among other things, lubrication challenges, creating imbalances, vibrations and premature failures
*This feature was written initially for Windpower Monthly and that it appears at the official WPM website!
WINDPOWER