The new-build ‘homes’ where energy scientists play God with the weather
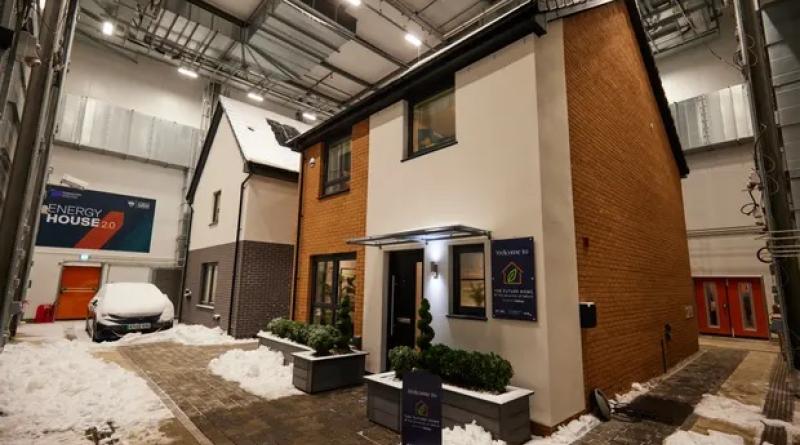
Researchers hope £16m temperature-controlled chamber can stress test green tech to help make houses energy efficient
The temperature is almost -6C and despite the snow, workers are frantically putting the finishing touches to a pair of detached houses that look ready to move into. But all is not as it seems in the energy industry equivalent of The Truman Show.
The new builds are nestled inside Energy House 2.0, a £16m temperature-controlled chamber at the University of Salford being unveiled on Thursday. It is hoped the research facility will play an important role in testing the technologies that will make our homes greener and cheaper to run, at a time when households are being crippled by sky-high energy bills.
Inside the chamber, scientists can play God, sending the temperature plummeting to -20C or to the shock high of 40C experienced for the first time in the UK last summer. They can also batter the houses with gale force winds or, courtesy of a snow machine, manufacture a blizzard to test its energy performance.
Richard Fitton, a professor in building performance at the University of Salford, says the initial research project – a partnership with UK housebuilders Bellway and Barratt Developments and the construction product manufacturer Saint-Gobain – would help to answer “difficult questions about how we reach zero carbon target in future housing”.
It comes as the industry gears up for government standards that require a significant reduction in carbon emissions for new-build homes from 2025.
“The facility will help us to stress test these buildings under extreme hot and cold climates to provide data on energy efficiency and overheating in homes,” says Fitton. “The buildings are in there for an initial period of two years but we will keep them for as long as they are useful. It goes against sustainability to knock buildings down.”
The chamber is housed within a “super-insulated” steel frame, plumbed with £6m of heating, ventilation and air conditioning equipment. Usually it takes months or years to collect the data needed to evaluate the performance of a new design or technology, but because researchers can precisely control the environment, they can gather that data in a few weeks.
Experiments scheduled for the coming months include having people “living” Big Brother-style inside them with access to facilities including flushable loos, showers, broadband and even Sky TV.
“This research will give me the answer to what are the best systems to put in new houses, including what happens when we put people inside … because that’s when it could all go a little bit off,” adds Fitton.
Unusually, perhaps, the small development features houses built side-by-side by rival builders, with Bellway and Barratt agreeing to share their findings at the end of the year-long project.
The eHome2 is a concept house devised by Barratt and Saint-Gobain. Next door, Bellway’s house, called the Future Home, is a three-bed detached property based on its Coppersmith model.
All UK properties on the market require a certificate outlining the energy performance, from A (most efficient) to G (least efficient). At the moment, the Coppersmith house has a B rating and running costs of £761 a year for heating, hot water, lighting, pumps and fans. By comparison, the Future Home is rated A, with running annual costs reduced to £11 thanks to the solar panels.
Compared with the bitter temperature outside, the Bellway home gives you a warm hug as you step inside, although it feels a bit topsy turvy as ultra-slim infrared radiators are perched on the ceiling rather than the wall and an air source heat pump has been stowed in the loft in what is a UK first. The windows are triple-glazed and upstairs there is a prototype shower that recovers heat from the wastewater.
Jamie Bursnell, Bellway’s group innovation and technical manager, says it is “treading on new ground here”, with the firm trying to “find the balance between lowering carbon emissions and keeping running costs as low as possible”.
The main difference between the two houses is that, while the Bellway house is built from “real” bricks, the Barratt one is a timber frame made of 36cm-thick insulation-filled panels covered in a thin cladding that mimics a brick finish.
The timber-frame house would secure a coveted A rating on an energy performance certificate, and Oliver Novakovic, Barratt’s technical and innovation director, says if you wanted to get the same energy efficiency in a traditional build the walls would need to be 55cm thick.
Two competing heating systems are being tested inside: an electric-based system utilising infrared panels, some of which are disguised as ceiling coving, as well as a water-based system that uses heated skirting boards combined with an air source heat pump.
“As we put these really warm coats on to our homes, we don’t need as much energy to heat them,” says Novakovic. “So the big question we’re asking is, do we do it with heat pumps and hot water or with electricity?” Experts will examine how houses can work in tandem with the electric car parked outside, for example storing energy produced by solar panels in the vehicle’s battery.
The university is also home to the original Energy House project, which built an early 20th-century two-up, two-down terrace house inside an environmental chamber to test retrofit technologies.
Prof Will Swan, the director of Energy House Labs at the University of Salford, described Energy House 2.0 as a “critical” piece of new research infrastructure.
“The growing challenges of climate change and the cost of living crisis mean we need to consider how we build and operate our homes,” says Swan. “As the cost of gas and electricity keeps going up and up this work is even more important to create a sustainable and economically viable future for this country and the world.”
COVER PHOTO: Detached homes at Energy House 2.0, the research facility at the University of Salford Photograph: Christopher Thomond/The Guardian