Britain to get first commercial refinery for extracting precious metals from e-waste.
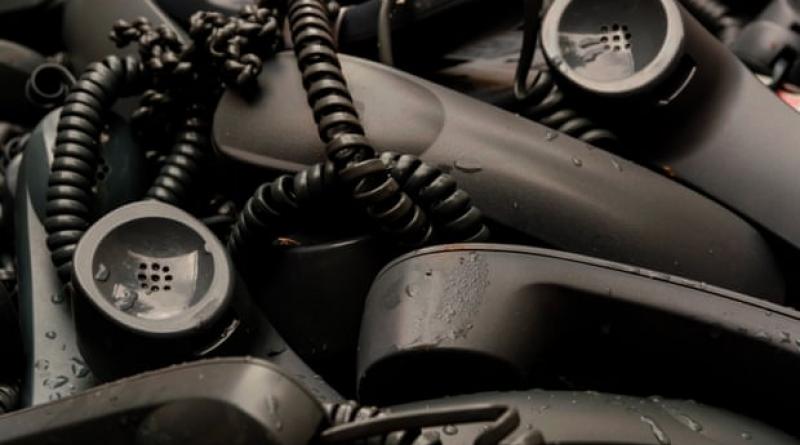
Cheshire-based facility will be world’s first to use bacteria-based recycling processes.
The UK is to get its first commercial refinery for extracting precious metals from electronic waste, which will also be the world’s first to use bacteria rather than cyanide-based processes.
A New Zealand startup, Mint Innovation, plans to open the facility within 12 months in Cheshire, in the north of England, after delays caused by the Covid-19 crisis.
The UK’s impending exit from the EU has provided an urgent economic need for such a facility – a UN report last month found at least $10bn (£7.9bn) of gold, platinum and other precious metals were dumped every year in a growing mountain of e-waste.
When the Commons environmental audit committee launched its inquiry into e-waste and the circular economy last year, its then chair, Mary Creagh, criticised the UK’s “unsustainable” approach to e-waste and called for radical action.
The UK produced more e-waste than the EU average and was “one of the worst offenders for exporting e-waste to developing countries ill-equipped to dispose of it in a socially and environmentally responsible way”, she said.
Recyclers in the UK have to send printed circuit boards to mainland Europe to have the precious metals they contain extracted. After Brexit, the costs of doing this are expected to rise.
Rhys Charles, a researcher at Swansea University’s College of Engineering, said: “If we have to pay import and export duties to access processes it could be detrimental to recycling at a time when it is becoming more strategically important to build our own circular economy.”
Mint was set up in 2016 to develop a bio-refinery that combines hydrometallurgy and biotechnology to safely extract metals – including gold, palladium, silver and copper – from e-waste.
Ollie Crush, the company’s chief scientific officer, says the key features of its refineries are that they are low-cost, green, and local to where the waste is being created.
“The plants are very agricultural, more like a small microbrewery. The regulatory tailwind is for western nations to handle their own waste stream. We offer the same yield as the big smelters, the same level of service and quicker,” he said.
“But unlike the smelters, we do not use cyanide and we use less energy, less CO2, less water, less waste. A refinery can be popped into any nation, region or city.’
The UK refinery will initially be able to process 20 tonnes of e-waste per day and, if the demand is there, this can be scaled up. Another plant in the south of England is being considered and a refinery is planned for Sydney, Australia.
Jason Love, a professor of molecular inorganic chemistry at Edinburgh University, says technical challenges need to be addressed if the mining of precious metals from electronic waste is to be truly sustainable and environmentally neutral.
He said: “What Mint is doing seems very nice but I don’t think it is groundbreaking. The real sticking point is how do you dissolve the metals. The company’s selling point is its use of microbes but that is only one aspect of its process. It is using acids too.”
Mint says it does not use cyanide but “common weak acids and a bit of tricky chemistry”. According to Crush: “From the start, it has been our intention to recycle as much of the chemicals we use as possible.”
Charles says if Mint can deliver it will be a game-changer. “Localised, smaller scale recovery benefits local people, they see the value of it to their community and town and so are more likely to buy into it. This is how you start to build truly sustainable economic development.”
22 August 2020
The Guardian