‘Big, Ambitious Action’ Needed to Decarbonize Cement
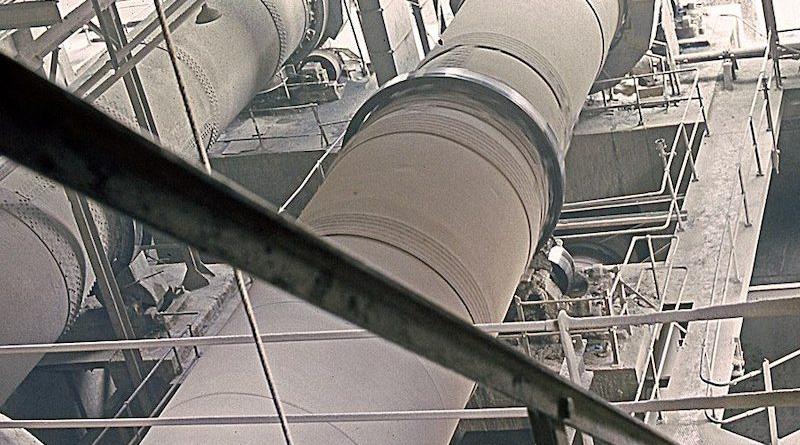
At least 30% of emissions produced by the cement industry could be eliminated right now with established technologies, but greening the sector completely calls for ambitious action on both the supply and the demand sides of the equation, say experts.
The chemical mysteries of ingredients, reliability concerns about alternatives, prohibitive costs, and a lack of demand are making decarbonization difficult for cement, “one of the building blocks of the modern world,” reports Canary Media, in a deep dive into the topic. But there’s no question that the cement industry needs to be decarbonized: if it were a country, the sector would rank third in the world for emissions after China and the United States, meaning that full decarbonization “will require big, ambitious action.”
A Least 30% Achievable Now
Swiss cement titan Holcim Group “has managed to chip away at its emissions in recent years,” says Canary Media. The company’s 2022 annual report claimed a 21% reduction in carbon emissions compared to 2021, thanks largely to material changes that reduced its use of “clinker,” an extremely carbon-intensive cement input that is responsible for the strength and durability of concrete.
Clinker’s creation process—which involves cooking limestone in a kiln at temperatures nearing 1,500°C—produces carbon dioxide as a waste product.
Enter the idea of reducing clinker and the quest for alternative fuels. “The math is fairly simple on clinker substitution,” Canary Media writes. “The greater the amount of clinker that’s substituted with another material, the lower the carbon footprint per tonne of cement that results.”
Portland limestone cement, which uses limestone that has been ground up rather than superheated, is currently the most popular substitute, followed by fly ash from coal plants and slag from steel mills.
But both of those latter inputs are time-limited, said Samuel Goldman, policy advisor at the United States Department of Energy (DOE) Loan Programs Office. In a fossil-free future, “they are not going to be available in the amounts required.”
Another factor adding to cement’s emissions footprint is the extreme heat the industrial process requires, which has traditionally relied on fossil fuels. Since 1995, the U.S. industry has cut its emissions per tonne of cement produced by about 10%, mostly be burning gas instead of coal or coke.
Replacing gas with waste-based fuels like old tires could reduce emissions by another 5 to 10% through 2030, Canary Media says. But the potential is limited, and deployment comes with supply and environmental constraints. Other possibilities, like electrification and clean hydrogen, remain “prohibitively expensive” or “technologically nascent.”
Which isn’t to say that the available decarbonization methods aren’t doing some pretty heavy lifting. “Oftentimes, people think we can’t do this because the technology isn’t there,” said Vanessa Chan, chief commercialization officer and director of DOE’s Office of Technology Transitions. “I think people should know that 30 to 40% of emissions can be abated from technologies that are ready today.”
The Stubborn 60%
Canary Media says dozens of research projects and start-ups are working on next-generation clinker substitutes, and some of them have reached the pilot stage. But overhauling the entire industry would begin with proof of concept in a single, integrated cement manufacturing plant—and that hasn’t happened yet.
That’s partly due to what Ryan Gilliam, CEO of alternative cement start-up Fortera, called the “incredible complexity” of cement chemistry and its real-world applications. “There are still fundamental debates among scientists,” he said, on whether one particular chemical reaction or another will yield better—or worse—forms of concrete, depending on the application.
For companies like Holcim, capturing and storing the carbon dioxide generated during limestone combustion remains the “No. 1 mid-term objective” for cutting process emissions. But the high capital cost of the equipment needed and the high energy cost of running it could add up to US$25 to $55 per tonne of cement produced, writes Canary Media.
That means “change at the scale required for the cement industry won’t come cheap, or fast.”
The American sector alone “will need to invest up to a cumulative US$20 billion by 2030, and a total of somewhere between $60 billion and $120 billion by mid-century,” writes veteran reporter Jeff St. John. “That’s a lot for an industry that made just under $15 billion in sales last year, and the necessary outlays are made more daunting by the fact that cement companies compete on razor-thin margins.”
‘Demand Signals’ for Green Cement
Cutting carbon from the sector will also require “demand signals,” or “clear mandates and incentives from cement buyers that reward the investments and risks” the industry will be taking. Governments could also play a key role, since “half of U.S. cement demand is driven by federal and state procurement,” said DOE’s Chan.
The Biden administration’s Buy Clean Initiative will help build and amplify the necessary demand signals, as will the low embodied concrete standards announced last year by the General Services Administration, which oversees about $75 billion in contracts per year.
PHOTO: Dylan Moore/Geograph