Australia must act quickly as overseas competition for green iron grows
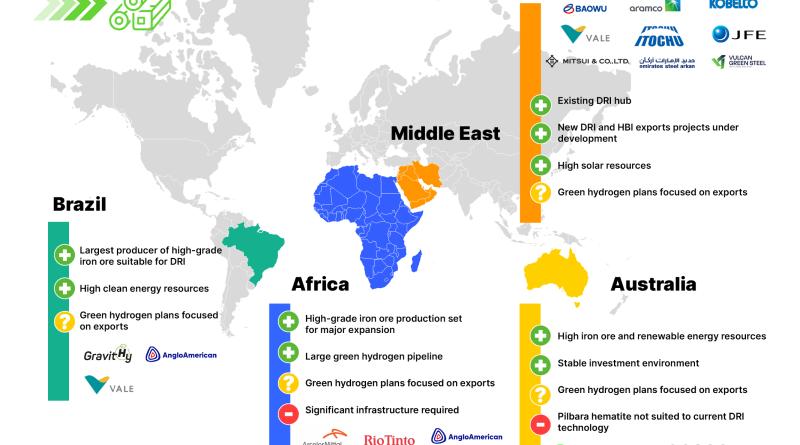
IEEFA Australia: Australia’s iron ore sector risks losing ground to other countries as they move to meet growing global demand for green iron, according to a new report from the Institute for Energy Economics and Financial Analysis (IEEFA).
As the global steel industry accelerates efforts to decarbonise its operations, it is shifting away from using coal-fuelled blast furnaces towards direct reduced iron (DRI) technology that can run on green hydrogen derived from renewable energy. This poses a significant challenge to Australia’s iron ore producers at a time when they face other long-term challenges including declining demand from their key export market, China, which is also aiming to reduce its reliance on imports from Australia.
A recent report from the Minerals Research Institute of Western Australia (MRIWA) found that a global steel industry shift away from coal towards DRI on a pathway to net zero emissions steelmaking presents “a material, structural change to Western Australia’s iron ore industry, and the economy more broadly”. It also highlighted that, in a scenario where the steel technology transition is accelerated, Western Australia’s iron ore industry would be “in a precarious position assuming no change to the current product mix”.
IEEFA’s report highlights the fact that the quality of the ore from Australia's major iron ore producing region, the Pilbara, mainly falls below direct reduction-grade (DR-grade), making it currently ill-suited to low-carbon steel production. This leaves Australia open to growing competition from places such as Brazil and Africa, which have abundant reserves of high-grade ore. In addition, the Middle East is already a hub for DRI-based steelmaking using natural gas and is well placed to switch to green hydrogen produced using the region’s abundant solar resources.
“All these areas are attracting interest from major steelmakers that are now planning long-term decarbonisation,” says Simon Nicholas, IEEFA’s Energy Financial Analyst Lead and the report’s co-author.
Green iron – made via DRI using green hydrogen and exported as hot briquetted iron (HBI) – is now being considered for import by major global steelmakers instead of importing both iron ore and green hydrogen, as part of decarbonisation plans for an industry currently based on the import of iron ore and metallurgical coal. In its assessment of options for Western Australia’s iron ore industry to position itself for a decarbonising steel sector, the MRIWA found that, “pathways which involve the development of intermediate iron products, such as HBI, are the most prospective for Western Australia.”
“Although Australia leads the world in iron ore exports, other nations and regions have the opportunity to combine their higher-grade iron ore and renewable energy resources to produce green iron in response to growing demand,” says Nicholas.
The report argues that Australia has numerous advantages in the race to lead the global steel sector into a low-carbon future, particularly renewable energy resources, good infrastructure and a stable investment environment. The Australian iron ore industry can position itself for a decarbonising steel sector by shifting towards onshore processing of iron ore using green hydrogen to produce low-carbon iron for export.
Crucially, Australia must rethink its strategy around green hydrogen. There is a growing focus on the development of a major green hydrogen production and export industry in Australia. However, the inefficiency and cost of shipping green hydrogen present significant obstacles for the direct export of hydrogen, while decarbonisation of areas such as residential energy supplies or road transport seem more likely to be achieved via electrification.
IEEFA’s report calls for more focus on using green hydrogen in domestic industrial sectors where it makes sense to do so, such as in the production of value-added products like green iron. As well as iron ore, the Pilbara is rich in renewable energy resources, meaning green hydrogen could be produced adjacent to the sources of ore that could then be processed via DRI for export as hot briquetted iron (HBI). This would be significantly more efficient than freighting both iron ore and hydrogen separately.
Australia must accelerate research and development that will allow the use of Pilbara iron ores in low-carbon ironmaking using DRI processes. This could include beneficiating Pilbara hematite iron up to DR-grade where possible, and a switch to more magnetite mining, which is more amenable to beneficiation up to a higher grade.
In addition, research into technology combinations that allow the use of Pilbara iron ore in DRI-based iron and steelmaking needs to be accelerated. Rio Tinto, Fortescue and BHP are all examining such technologies.
“Because of the scale of Australian iron ore exports, the global steel sector will need Australian iron ore to be heavily involved in decarbonisation if net zero global steel emissions are to be achieved,” says Soroush Basirat, Energy Finance Analyst, Steel Sector and the report’s co-author. “However, our report shows that Australia has to address these challenges if it is to remain the global iron ore leader in a decarbonising world and not lose out amid growing demand for low-carbon iron and steel.”
Read the report: Australia faces growing green iron competition from overseas